From Nano to Macro
Eva Kollmannsberger and Anton Nischler are confident that “what we are working on today will become increasingly important in the future.” Both doctoral candidates have been working for over two years as research assistants at the Competence Center for Lightweight Design (LLK) at Landshut University of Applied Sciences. While Kollmannsberger is working on the development of high-temperature-resistant iron aluminides, Nischler is examining the fatigue lifetime of wrought magnesium alloys in order to find out and to be able to predict when a component will be fatigued or fail – a basic requirement for the design of lightweight structures for the automotive industry for example.
What we are working on today will become increasingly important in the futureEva Kollmannsberger and Anton Nischler, Doctoral Candidates at the LLK
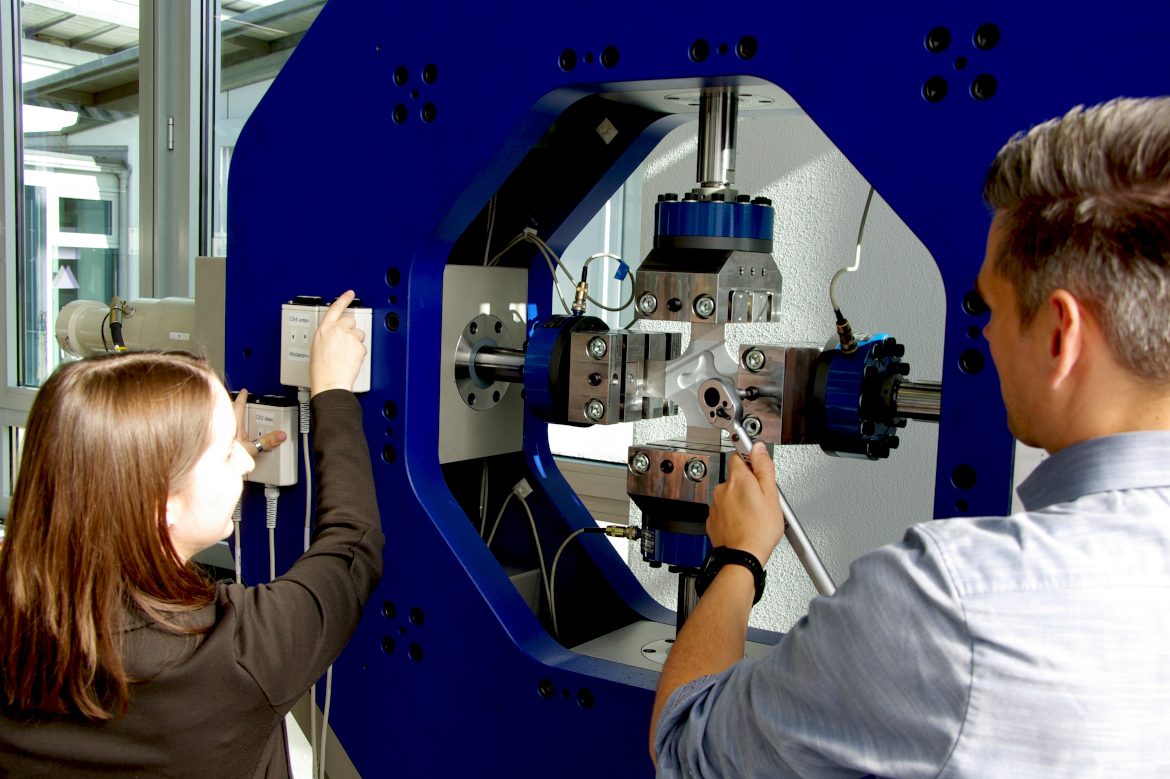
Virtual Component Development
Lightweight design for the sustainable use of resources is a key topic across many sectors. The aim is to save weight using lighter materials and innovative designs and technologies for the more efficient use of raw materials and energy and in order to increase the load capacity. Wrought magnesium alloys are among the light materials which are the focus of the Lightweight Design research project.
It is funded by the Free State of Bavaria and under the lead of Professor Otto Huber. Nischler is working on a computer-aided stress analysis for Mg-alloys in order to predict where the weaknesses of a component lie and how long it will withstand the stresses. In the future, this tool should support the development process of hot formed Mg-structures.
At the same time, the PhD candidate is conducting real tests on the biaxial testing machine in order to characterise the deformation behaviour of the material under multiaxial stresses. “These test stations for static and cyclic tension and compression tests, with two axles arranged at 90° to each other, are very rare,” explains Huber, who founded the Institute in 2002, “such tests are usually conducted only uniaxially.”
The Institute offers extremely attractive conditions with the high-quality equipment in our four laboratories.Professor Otto Huber, Head of Project "Lightweight Design"
High-Tech Material Analysis
A further research project called “FeAl-GuD” under the lead of Professor Holger Saage examines the material properties of iron aluminium for combined gas and steam power plants. Here, Eva Kollmannsberger is conducting research into the structure of her material samples with the aid of nano computer tomography (nCT) and the scanning electron microscope in the Material Analytics Laboratory.
“My work focuses on the creep and fatigue behaviour of intermetallic iron aluminides. I am examining the effects of thermal and mechanical stresses on the material. With the aid of the scanning electron microscope and the CT, I can assess whether anything and what has changed inside my material during the tests. Transformations in the material can occur especially under thermo-mechanical stress,” explains the PhD candidate. “I want to find out how the material can be optimised by adding compounds such as carbide and borides in order to make it easier to machine and withstand higher stresses.”

High-Quality Laboratory Equipment
Conducting research alongside Huber and Saage are Professors Hubert Klaus, Walter Fischer, Norbert Babel, three further research assistants, and four laboratory staff—all at the LLK, which is located in the Faculty of Mechanical Engineering at Landshut University of Applied Sciences. “The Institute offers extremely attractive conditions for our PhD students with the high-quality equipment in our four laboratories. Here we cover the entire multi-scale chain from material analytics, characterisation and mechanics to structural mechanics and design, and to the production and testing of lightweight structures made out of metals and polymers as well as composite materials,” explains Huber.
The doctoral candidates are also supported by students on the Master’s degree courses Lightweight Design and Simulation (consecutive programme) and Applied Computational Mechanics (part-time, work-based degree), who contribute energetically to the research through their project work, theses, and/or as student assistants. A further benefit for doctoral candidates: The young researchers gain teaching experience, which will be of use to them in future.
To know that you can be a pioneer and develop something which has never existed before is a great feeling.Eva Kollmannsberger, Doctoral Candidate at the LLK
Cooperation with Industry and Research Partners
The LLK cooperates closely with industry in application-oriented research projects, in particular with small and medium-sized companies, as well as with OEMs. The close cooperation with the University's lightweight design cluster also provides a good opportunity for young scientists to build their own networks with other research institutes and industry – as cooperation partners or potential future employers.
“The topic of lightweight design is currently of great interest in particular to the aviation, automotive and commercial vehicle industries due to the requirements to reduce CO2 emissions,” explains Huber, “but is also increasingly attracting attention in many other industries such as the mechanical engineering, medical technology, furniture and leisure industries.”
Working at a University of Applied Sciences
- What is a University of Applied Sciences?
- Getting to know Universities of Applied Sciences as a visiting researcher
- Doing your PhD or becoming a professor at a University of Applied Sciences
Research Topics of the Future
At the same time, the LLK maintains close partnerships with other research institutes. In close cooperation with the University of Salzburg (PLUS), a joint cross-border Research and Development Centre for Lightweight Design has been established. Nischler is doing his doctorate in cooperation with Freiberg University of Mining and Technology, while Kollmannsberger is studying for her doctorate at RWTH Aachen University.
The two young researchers do not yet know what they will do when they have completed their studies. “My project has another two years to run, but I can imagine staying in research long term,” reflects Nischler. “I find it really exciting to work on something completely new and to be creative.” His colleague adds: “you never know what the end result is going to be. But to know that you can be a pioneer in a field and develop something which has never existed before is a great feeling.”
International scientists and those completing internships who would like to get to know the Development Center for Lightweight Design during a guest stay are always welcome. Bachelor and master theses are also offered. Knowledge of German is an advantage, but not absolutely necessary.
Further information about the LLK and Landshut University of Applied Sciences can be found at www.kompetenzzentrum-leichtbau.de and www.haw-landshut.de